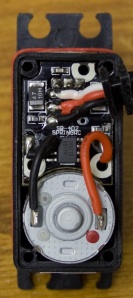
A DC motor is the standard electric motor; it will spin as fast as it can with the DC power you provide it with. On its own, a DC motor has no position control. Most DC motor controllers allow you to change the duty cycle, a value from 0 to 100% that describes how much of your power supply is being made available to the motor.
A servo motor is just a DC motor with some upgrades: they typically have a gearbox to increase output torque, and they have a control system built right inside the motor’s casing. Since all of the control is built in, you can simply tell a servo to rotate to a specific angle, and it’ll try its best to move to that position. The downside to an integrated control system is that you usually can’t customize it in any way.
A best stepper motor uses alternating current through two separate coils to turn the rotor. I won’t go into the details, but the end result is that the motor moves in distinct “steps”, and the angle of these steps can be calculated from the step angle listed on the motor’s datasheet and the gearbox reduction ratio, if it has a gearbox. Since the motor turns a known amount each time a step is made, the position and velocity can be calculated.
1.8° NEMA 8 GEARED STEPPER MOTOR WITH PLANETARY GEARBOX
Four types of waveforms and sequences drive for stepper motors
Aucun commentaire:
Publier un commentaire